Production Manager
The opportunity
Manufacturing Production Workers focus on setting up, operating, maintaining, and troubleshooting manufacturing production (i.e., machining, processing, assembly, or packaging) equipment including: Operating machine tool, chemical processing, assembly, or packaging equipment to manufacture products according to production specifications, schedules, volume/cost/wastage targets, and quality standards. Moving, packing, and sorting raw materials or finished goods. Monitoring the quality of output to identify, discard, or re-manufacture faulty products. Maintaining accurate daily production records as input to manufacturing performance analysis A Team Leader supervises para-professional employees. Responsibilities typically include: Setting day-to-day operational objectives for team. Problems faced may be difficult but typically are not complex. Ensures policies, practices and procedures are understood and followed by direct reports, customers and stakeholders.
How you'll make an impact
- Implements Health, Safety & Environment (HSE) and business compliance standards, process and regulations within the units. Identify unsafe operations, SOT process, hazards identification and implement the process for compliance.
- Responsible for the Production Function, Team coordination for demand & supply management, inventory management, WIP management and control, suppliers coordination for quality & material supply issues.
- Generating production documentations such as assembly / work instructions, Safe operating procedures/process. Production forecast, planning, scheduling, target setting and resources management, team building and training.
- Tracking production KPIs to meet targets, FPY, on-time and on- cost, assembly cycle time, requested on-time delivery (ROTD), cost reduction and production down time.
- Assembly line setup, resource optimization and improvements, capex management. Stores management, dispatch and logistics management.
- Perform engineering analysis to reduce downtime, re-work optimization and plan preventive maintenance. Implementing Poka-Yoke wherever possible to prevent errors.
- Carry out FMEAs, (Failure Mode Effects Analysis) process documentation and implement improvements. Investigate production and process issues, change management and providing technical solution and training.
- Conduct benchmarking studies to determine best practices/designs and future trends. Support and lead continuous improvement programs, problem solving and process improvement activities. Shares functional best practices and lessons learned across the organization.
- Implementing and ensuring compliance with global and local standards, rules, tools, policies which are related to production process.
- Resolution Process (CCRP), Internal Transactional Partnership Survey (ITPS), Top 5 Quality Initiatives (T5QI) and other voice of the customer initiatives. Evaluate current production activities and make recommendations for improvements.
- Responsible to ensure compliance with applicable external and internal regulations, procedures, and guidelines.
- Living Hitachi Energy's core values of safety and integrity, which means taking responsibility for your own actions while caring for your colleagues and the business
Want more jobs like this?
Get jobs in Chennai, India delivered to your inbox every week.
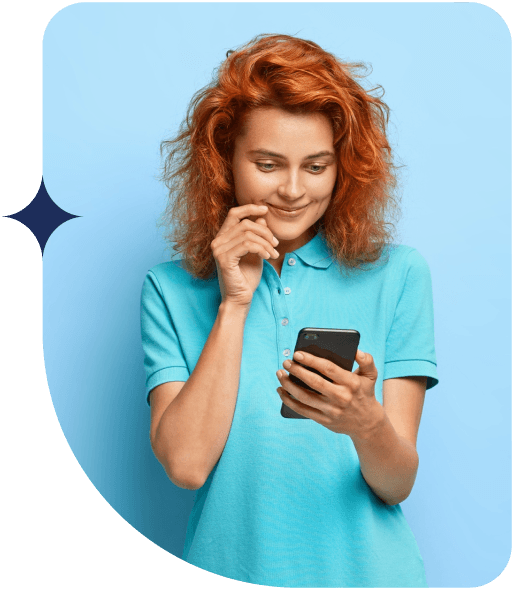
Your background
- Candidate should hold a degree in BE / B.Tech Electrical / Electronics /Mechanical/Manufacturing and Postgraduation in production engineering is an added advantage.
- Having minimum 10 years of experience in assembly and production of Power electronics and associated production line or process, out of which min 5 years in leadership role.
- Expertise on SAP PP module is must, preferred as power user. Expertise on Lean manufacturing tools like 6S, Six Sigma, Gemba, Kaizen, Kanban, Poka Yoke, TPM etc. Understanding of Health and Safety practices.
- Ability to train the work group and lead teams within the work group Ability to manage group to achieve goals within budget. Understanding of manufacturing /assembly processes.
- Understanding of Electrical Symbols, Schematic and Mechanical drawings. Understanding engineering, scientific and other technical information. Shop floor layout and cell or workstation designs. Design of fixtures and tooling for assembly tasks.
- Planning and prioritizing activities Lean manufacturing. Ability to present data effectively, Strong problem-solving skills and logical approach. Team working and Analytical skills. Excellent negotiation skills
- Good understanding of customer expectations and deliverables with an awareness of the impact of failure/cost of poor quality.
- Proficiency in both spoken & written English language is required
Apply now
Current employees apply here
Perks and Benefits
Health and Wellness
- Health Insurance
- Dental Insurance
- Vision Insurance
- Life Insurance
- Short-Term Disability
- Long-Term Disability
- FSA
- HSA With Employer Contribution
- Pet Insurance
- Mental Health Benefits
- Virtual Fitness Classes
- On-Site Gym
Parental Benefits
- Fertility Benefits
- Family Support Resources
- Birth Parent or Maternity Leave
- Adoption Assistance Program
Work Flexibility
- Flexible Work Hours
- Remote Work Opportunities
- Hybrid Work Opportunities
Office Life and Perks
- Commuter Benefits Program
- Snacks
- Some Meals Provided
- Company Outings
- Holiday Events
Vacation and Time Off
- Paid Vacation
- Unlimited Paid Time Off
- Paid Holidays
- Personal/Sick Days
- Summer Fridays
Financial and Retirement
- 401(K) With Company Matching
- Performance Bonus
- Relocation Assistance
- Financial Counseling
Professional Development
- Tuition Reimbursement
- Learning and Development Stipend
- Promote From Within
- Mentor Program
- Access to Online Courses
- Lunch and Learns
- Work Visa Sponsorship
- Leadership Training Program
- Internship Program
- Associate or Rotational Training Program
Diversity and Inclusion
- Diversity, Equity, and Inclusion Program
- Employee Resource Groups (ERG)
Company Videos
Hear directly from employees about what it is like to work at Hitachi Energy.