Shift Performance Manager
Position Description
Job Summary
POSITION SUMMARY
This position will provide the leadership to effectively lead all shift operation efforts in a manner to achieve maximum production, operating and shipping efficiencies within safety, quality, service and cost standards; will be responsible for shift production and maintenance performance; will be responsible for all site activities outside normal business hours and on weekends, and is accountable for improving the applicable standards in the plant. The Seattle Manufacturing Facility has three primary production areas (Line 1, Line 2, Stucco Preparation Area), with a total capacity of 600 MMSF, including a 24 hour per day shipping operation.
ESSENTIAL DUTIES
- Has extensive latitude for non-reviewed actions and the exercise of independent judgment and discretion within established policies and procedures
- Manages direct labor cost/variances for shift through scheduling based on production volumes.
- Ensures raw material usages are in agreement with product BOM's
- Ensures all shift processes meet applicable financial Internal Control guidelines for inventory controls, including completing entry for production and shipping data input, quality holds
- Ensures the shift is operating within all legal, compliance and applicable contractual policies and procedures
- Responsibility for providing an accident-free workplace by improving Health & Safety conditions and performance on the shift, including; training employees, scheduling risk assessments and related actions, actively promoting behavioral safety processes, use of Safety Management Audit Tool (SMAT) and Observational Safety Audit (OSA) audit usage and compliance, incident investigation and follow up, incident reporting using standard forms and procedures
- Responsibility for product quality control on all production lines on shift, including Compliance of product quality checks with control plans; auditing of quality control plan compliance, implementation of new quality procedures; management of defective product within existing procedures; investigation into quality check non-compliance, customer complaints and subsequent actions, participation in product & process trials
- Assures good housekeeping practices (5S) through auditing, enforces plant rules and safety regulations
- Reports accurate production numbers and issues faced through GXO and other systems
- Reports gaps in Bill of Materials (BOMs).
- Continuously evaluates shift performance to identify gaps and focuses on continuous improvement in areas of opportunity/non-compliance and develops the shift skills and competences
- Guides and promotes employees to participate in improvement projects, using WCM improvement tools (Focused Improvement, Autonomous Maintenance, People Development and Quality improvement tools), in partnership with Production and Line Improvement Managers, to meet milestones in accordance with the Manufacturing Business Plan and plant project savings plan (F-Matrix)
- Ensures shift use of the standard Emergency Work Order (EWO)/Quick Kaizen process to ensure problem root causes are identified and losses are accurately reported, and improvements achieved • Provides input for new equipment (Early Equipment Management) projects to line improvement teams
Want more jobs like this?
Get Software Engineering jobs in Seattle, WA delivered to your inbox every week.
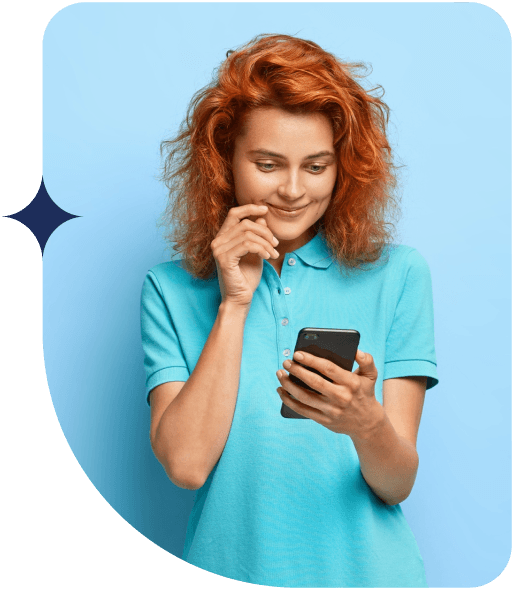
Required Qualifications
MINIMUM KNOWLEDGE AND SKILLS REQUIRED
- Bachelor's Degree in engineering, science, industrial management, or similar discipline, or five (5) years of equivalent training and experience that provides a comprehensive working knowledge of the laws, regulations, practices and procedures of a Lean/World Class Manufacturing operation may be substituted for a degree
- Six to eight (6-8) years of applied professional experience working in production in an industrial /manufacturing environment
- Three to four (3-4) years of direct or indirect supervisory experience
- Familiarity with Lean / World Class principles and practices
- Ability to provide leadership and innovation at all levels of the organization utilizing differing styles of management and communication; from directive, to coaching and support, through delegation, as the situation arises
PREFERRED OR DESIRED QUALIFICATIONS
- Bachelor's degree in an engineering field
- Ten (10) years of applied professional production experience with specifically 4 years' experience in direct supervision, employee relations and scheduling
- World Class Manufacturing (WCM) Instructor or similar qualification
- Previous experience in gypsum industry
- Proven ability to be an outstanding coach and leader, with succession planning and employee development skills
- Advanced Microsoft Office Suite proficiency and familiarity with JD Edwards and/or SAP software
Legal Statement
Saint-Gobain provides equal employment opportunities (EEO) to all employees and applicants for employment without regard to race, color, religion, sex, gender, sexual orientation, gender identity or expression, national origin, age, disability, genetic information, marital status, amnesty, or status as a covered veteran in accordance with applicable federal, state and local laws. Saint-Gobain is an equal opportunity employer of individuals with disabilities and supports the hiring of veterans.
Perks and Benefits
Health and Wellness
Parental Benefits
Work Flexibility
Office Life and Perks
Vacation and Time Off
Financial and Retirement
Professional Development
Diversity and Inclusion